Oil field economics are changing rapidly. As a way to save money and reduce environmental impacts, many oil producers are using multi-well pad drilling as an alternative to single well sites. In 2014 over half of all new wells in unconventional fields were done using multi-pad drilling sites. Over the life of a well, different types of artificial lift equipment may be employed to maximize production. Unfortunately, with more wells, there is an increase in harmonics, and also in voltage distortion. This is presenting a problem for many multi-well pad drilling sites.
A field operator in the Bakken called upon TCI to find the best solution for reducing the costs of mitigating these harmonic issues over the lifetime of their site.
Assessing the Situation
The customer’s site was a multi-well pad with 18 wells that could transition through various artificial lift technologies over their lifecycle. If single well solutions are used, each time that a pump change was made to the site, new harmonic filters were required. This field operator was looking for a single solution that could handle all of their harmonic needs throughout the lifecycle of the site. The operator contacted TCI for assistance in solving their significant harmonic current and high background voltage distortion problems.

In looking for an answer, it was seen that the traditional single well approach was not optimal for multi-well pads. The single well approach does not use the point of common coupling (PCC) at the transformer feeding the pad, it isn’t flexible enough to support lifecycle changes, and it has high costs because there is little reuse of harmonic solutions.
TCI engineers found that the best solution to the harmonic current and voltage distortion problems was to install one HarmonicGuard Active Filter (HGA) at the PCC.
Over the lifetime of multi-well pads, a single HGA can replace multiple passive harmonic filters, multi-pulse drives, or active front end drives. Throughout the pads lifecycle, TCI’s HarmonicGuard Active Filter solution enables the use of simple, quick ship, six-pulse VFDs. The HGA is a one-time installation with one disconnect per site. The HGA is IEEE-519 Compliant at the point of common coupling. It is a shunt device, which means that a fault in the filter will not halt the VFD operation and oil production.
Active harmonic filters that mitigate harmonics and improve power factor provide an economic solution to the multi-well pad application. The HGA provides greater cost savings compared to an integrated single well VFD solution like an eighteen-pulse drive or an active front end drive.
Summary
Voltage distortion can be effectively reduced to acceptable levels using harmonic filters. A basic understanding of how distortion is created and the effects of circuit impedances helps in resolving the problems created by distortion.
Realizing the role of the distribution system architecture and points of common coupling in any installation can enable the optimization of harmonic solutions. Just one of TCI’s HarmonicGuard Active Filters can replace multiple passive harmonic filters, multi-pulse drives or active front end drives in a multi-well pad. The HarmonicGuard Active Filter can reduce harmonic mitigation costs over the lifetime of a site due to application at the PCC and its immunity to background voltage distortion.
HGA filters are available in outdoor (3R) as a standalone product, indoor (Type 1) for use inside e-houses or as open panels.
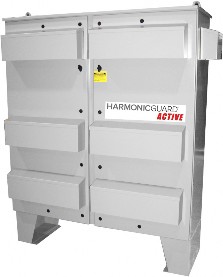
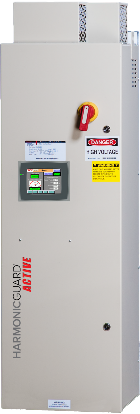
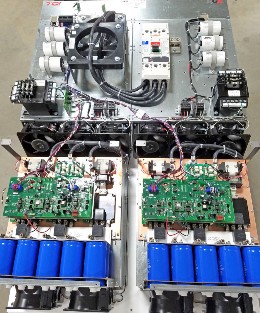